Luft im Allgemeinen
Luft ist ein farb-, geruch- und geschmackloses Gasgemisch. Es besteht aus vielen verschiedenen Gasen. Die Hauptbestandteile sind Sauerstoff und Stickstoff. Luft kann bei den meisten Berechnungen als ideales Gas betrachtet werden.
Die Zusammensetzung ist bis zu einer Höhe von 25 km über dem Meeresspiegel relativ konstant.
Luft enthält immer auch feste Partikel, wie Staub, Sand, Ruß und Salzkristalle.
Während die Menge dieser Partikel in bewohnten Gegenden höher ist, nimmt sie in ländlichen Gebieten und in großer Höhe ab. Luft ist aber keine Chemikalie, sondern lediglich ein Gasgemisch.
Dies ist auch der Grund dafür, warum Luft durch eine starke Abkühlung wieder in ihre Bestandteile zerlegt werden kann.
Feuchte Luft
Feuchte Luft kann als Mischung aus trockener Luft und Wasserdampf angesehen werden.
Enthält Luft Feuchtigkeit, wird diese auch als feuchte Luft bezeichnet. Die Luftfeuchtigkeit kann zwischen verschiedenen Grenzen schwanken. Die Extremwerte sind vollständig trockene und vollständig gesättigte Luft.
Die Fähigkeit der Luft, Wasserdampf aufzunehmen, nimmt mit steigender Temperatur zu. Es gibt somit zu jeder Temperatur eine maximal mögliche Wasserdampfmenge, die in der Luft enthalten sein kann.
Luft enthält normalerweise deutlich weniger Wasserdampf als maximal möglich.
Die relative Feuchtigkeit, angegeben in Prozent, gibt den Sättigungsgrad der Luft mit Wasserdampf für eine bestimmte Temperatur an. Der Taupunkt ist die Temperatur, bei der die Luft vollständig mit Wasserdampf gesättigt ist. Fällt die Temperatur der Luft unter den Taupunkt, setzt Kondensation ein. Der Begriff des atmosphärischen Taupunktes wird dann verwendet, wenn die Luft vollständig entspannt ist. Der Drucktaupunkt gibt denselben Wert für verdichtete Luft an.
Es gilt der folgende Zusammenhang:
Kompressorenarten
Es existieren zwei grundsätzlich verschiedene Methoden zur Verdichtung von Luft oder anderen Gasen, das Verdränger Prinzip und das Turboprinzip. Bei den Verdränger Kompressoren unterscheidet man zwischen Kolben- und unterschiedlichen Arten von Rotationsverdichtern. Sie sind die am häufigsten eingesetzten Kompressoren.
Weshalb Druckluftaufbereitung?
Die vom Kompressor angesaugte und verdichtete Luft enthält neben einem großen Wasserdampfanteil auch Verunreinigungen anderer Art wie Ölaerosole, Staub, Bakterien u.v.a.
Diese Verunreinigungen können hervorrufen:
- Korrosion und Verschmutzung im Leitungsnetz
- Druckverluste durch verunreinigte Rohrleitungen
- höherer Verschleiß durch verminderte Schmierung an Pneumatik Elementen
- Ausschuss oder Betriebsausfall an den Produktionsmaschinen
- Ausschuss an Lackieranlagen u.v.m.
Alle diese Störungen kosten sehr viel Geld - ein Vielfaches des Aufwandes für eine optimal angepasste Druckluftaufbereitung.
Methoden der Drucklufttrocknung
Die unterschiedlichen Verfahren der Drucklufttrocknung können hinsichtlich der erreichbaren Drucktaupunkte und der hierzu notwendigen Energie unterteilt werden. Je nach Trocknungsprinzip wird der Energiebedarf in Form von Druckluftverbrauch oder als elektrischer Energiebedarf abgedeckt. Prinzipiell gilt, je trockener die Druckluft sein muss, desto teurer ist die Trocknung.
Daher sollte die Druckluft nur so weit getrocknet werden, wie es für die Verbraucher notwendig ist. Für die Drucklufttrocknung stehen verschiedene Trocknungsmethoden zur Verfügung:
- Auskondensierung durch Kältetrocknung
- Adsorption
- Absorption
- Diffusion
Am häufigsten werden in der Drucklufttechnik Kältetrockner, Adsorptionstrockner und bei kleineren Mengen auch Membrantrockner eingesetzt.
Kältetrocknung
Die Kältetrocknung beruht auf der mit abnehmender Temperatur abnehmenden Fähigkeit der Luft, Wasserdampf zu binden. Im Gegensatz zu kaltwasserbetriebenen Zwischenkühlern oder Nachkühlern werden Kältetrockner mit einem Kühlmittel in einem geschlossenen Kältekreislaufbetrieb. Die einströmende feuchte Druckluft wird zunächst im Gegenstrom zur abströmenden getrockneten Druckluft abgekühlt. Anschließend wird der Luft über den Kältekreislauf weitere Wärme entzogen, bis der gewünschte Drucktaupunkt erreicht ist.
Danach erfolgt im Gegenstrom-Wärmetauscher die Rückerwärmung bis nahe dem Eintrittszustand. Da die Druckluft zur Vermeidung von Eisbildung nicht unter 0 °C abgekühlt werden kann, ist der Einsatzbereich dieses Verfahrens zwar begrenzt (Drucktaupunkt bis herab zu ca. +3 °C), jedoch in den meisten Anwendungsfällen ausreichend.
Adsorptionstrocknung
Diese Trockner arbeiten nach dem Prinzip der Oberflächenadsorption. Wassermoleküle lagern sich an der Oberfläche des Trockenmittels an und werden durch Adhäsionskräfte gehalten.
Da sich das Trockenmittel (meist Silica-Gel, Aluminiumoxid, Molekularsiebe) während des Trockenvorgangs mit Feuchtigkeit anreichert, ist eine Regeneration erforderlich.
Zur Regeneration des Trockenmittels wird bei der sog. Warmregeneration erwärmte Luft durch das Trockenmittel geführt. Hierzu gibt es verschiedene Schaltungsvarianten, bei der die Wärme separat erzeugt wird (z.B. elektrisch) oder die in der Druckluft enthaltene Wärme verwendet wird (besonders bei trockenlaufenden Verdichtern).
Das letztere Verfahren ist besonders wirtschaftlich, da nur eine minimale elektrische Anschlussleistung benötigt und zugleich die Verdichter Abwärme sinnvoll genutzt wird. Weiterhin steht dem Verbraucher die volle Druckluftmenge ohne Spülverluste zur Verfügung.
Ein Nachteil des Verfahrens besteht allerdings in der Begrenzung des minimal erreichbaren Drucktaupunkts auf ca. -30 °C.
Bei der Kaltregeneration wird ein Teilstrom der entfeuchteten Druckluft (10-20%) im entspannten Zustand zur Regeneration des Trockenmittels abgezweigt. Die erforderliche Mindestmenge, die zur Regeneration abgezweigt werden muss, ist vom Betriebsdruck und der Wasserbeladung der Luft abhängig. Da die Regenerationsluft in diesem Fall vom Kompressor erst erzeugt werden muss, ist dies für die Wirtschaftlichkeit des Trockners ein ausschlaggebender Faktor.
Adsorptionstrockner bestehen i.d.R. aus zwei mit Trockenmittel gefüllten Behältern oder zwei voneinander getrennten Behälterbereichen, die wechselseitig mit feuchter Druckluft beaufschlagt werden. Während in einem Behälter (-bereich) die Luft getrocknet wird, findet in den anderen Behältern (-bereich) die Regeneration des Trockenmittels statt. Die Zyklen können fest oder belastungsabhängig gesteuert werden. Zum Einsatz kommen Adsorptionstrockner dort, wo sehr geringe Restfeuchten (Drucktaupunkt bis -80 °C) erforderlich sind, die den Einsatz von Kältetrocknern ausschließen.
Absorptionstrocknung
Die Trocknung durch Absorption ist ein chemischer Vorgang, bei dem Wasserdampf durch eine chemische Reaktion vom Absorptionsmittel aufgenommen wird. Die Absorption kann mit festen (z.B. Salze) oder flüssigen (z.B. Glykol, Glycerin) Absorptionsmitteln durchgeführt werden. Je nach eingesetztem Mittel ist eine externe Regeneration durch Warmluft und Wiederverwendung möglich. Der Einsatzbereich dieses Verfahrens überschneidet sich mit dem des Adsorptionsverfahrens, allerdings sind entsprechend geringe Restfeuchten nicht erzielbar.
Membrantrocknung
Der Membrantrockner ist eine Ergänzung und Alternative zu den angestammten Kälte- und Adsorptionstrocknern. Die spezifischen Kosten für die Trocknung der Druckluft sind im Vergleich zu den anderen Systemen sehr hoch. Vor allem als Endstellentrockner, für kleinere Druckluftmengen, nicht kontinuierlichem Betrieb oder Anwendungen ohne elektrische Energie hat sich der Membrantrockner bewährt. Herzstück dieser Membrantrockner sind die Polymer-Hohlfasermembranen, die den in der Druckluft befindlichen Wasserdampf leicht hindurch diffundieren lassen. Die zuverlässige Funktion des Membrantrockners hängt wesentlich von der Filtration ab. Ein regelmäßiger Wechsel der Filterelemente ist somit zwingend erforderlich.
Partikel > 1µm und flüssiges Kondensat müssen sicher abgeschieden werden und ein Restölgehalt von max. 0,01 mg/m3 ist Grundlage für einen langjährigen und zuverlässigen Betrieb.
Je nach Anforderung sind Absenkungen des Drucktaupunktes (DTP) um wenige K als auch sehr weite Drucktaupunktabsenkungen bis zu 55 K möglich (z.B. von 35 °C auf –20 °C). Der Spülluftverbrauch ist je nach DTP-Absenkung zwischen 9 und 30% der eintretenden Druckluft. Da Membrantrockner meist im kleinen Leistungsbereich angesiedelt sind (bis 2 m 3/min), ergeben sich auch bei diesen prozentual geringen Verbräuchen in Bezug auf die gesamte Drucklufterzeugung geringe Betriebskosten.
Bewertungskriterien der unterschiedlichen Systeme aus energetischer und wirtschaftlicher Sicht
Die Betriebskosten für die verschiedenen Trocknerarten sind sehr unterschiedlich, wie die folgende Abbildung zeigt.
Die Kosten für die Drucklufttrocknung resultieren zum großen Teil aus den Energiekosten. Diese können direkt durch den Trockner verursacht werden (z.B. Antrieb des Kälteaggregats eines Kältetrockners) oder indirekt in Form von Spülluftverlusten wie bei einem kaltregenerierten Adsorptionstrockner.
Steht ein trockenlaufender Verdichter zur Verfügung, sollte unter dem Betriebskostenaspekt auf jeden Fall dem warmregenerierten Adsorptionstrockner mit Wärmerückgewinnung der Vorzug gegeben werden. In allen anderen Fällen sollte, wie aus Abb. oben deutlich hervorgeht, wo immer möglich ein Kältetrockner eingesetzt wird.
Druckluftqualität
Die ISO 8573-1 ist die Hauptpublikation der ISO 8573- Normenreihe, da darin die zulässige Schmutzstoffmenge pro Kubikmeter Druckluft festgelegt ist.
In der ISO 8573-1 werden Feststoffpartikel, Wasser und Öl als primäre Schmutzstoffe genannt. Die Reinheitsgrade der einzelnen Schmutzstoffe sind separat in tabellarischer Form aufgeführt. Aus Gründen der Nutzerfreundlichkeit sind in diesem Dokument jedoch alle drei Schmutzstoffe in einer übersichtlichen Tabelle zusammengefasst.
Angabe der Luftreinheit in Übereinstimmung mit ISO8573-1:2010
Bei der Angabe der erforderlichen Luftreinheit ist stets die Norm anzugeben, gefolgt von der für die einzelnen Schmutzstoffe ausgewählten Reinheitsklasse (bei Bedarf kann für jeden Schmutzstoff eine unterschiedliche Reinheitsklasse angegeben werden). Nachstehend ist die Angabe der Luftqualität beispielhaft dargestellt:
ISO8573-1:2010, Klasse 1.2.1
ISO8573-1:2010 verweist auf das Normdokument und dessen Fassung. Die drei Ziffern geben die für Feststoffpartikel, Wasser und den Gesamtanteil des Öls festgelegte Reinheitsklassifikation an. Mit der Reinheitsklasse 1.2.1 wird für den Betrieb unter den Referenzbedingungen der Norm folgende Luftqualität angegeben:
Partikel Klasse 1
Die Partikelanzahl pro Kubikmeter Druckluft darf 20.000 im Bereich 0,1 - 0,5 Mikron, 400 Partikel im Bereich 0,5 - 1 Mikron und 10 Partikel im Bereich 1 - 5 Mikron nicht überschreiten.
Wasser Klasse 2
Gefordert ist ein Drucktaupunkt (DTP) von -40 °C oder besser. Wasser in flüssiger Form ist nicht zulässig.
Öl Klasse 1
Pro Kubikmeter Druckluft sind maximal 0,01 mg Öl zulässig. Bei diesem Wert handelt es sich um den Gesamtgehaltan flüssigem Öl, Ölaerosolen und Öl Nebel.
ISO 8573-1:2010 Klasse 0
- Bei Klasse 0 sind keinerlei Schmutzstoffe zulässig.
- Bei Klasse 0 müssen Benutzer und Gerätehersteller im Rahmen einer schriftlichen Spezifikation Verunreinigungsgrade festlegen.
- Die vereinbarten Verunreinigungsgrade einer Spezifikation der Klasse 0 müssen innerhalb des Messbereichs der in ISO8573 Teil 2 bis 9 angegebenen Testausrüstung und -methoden liegen.
- Die vereinbarte Spezifikation der Klasse 0 muss normkonform schriftlich auf allen Dokumenten vermerkt werden.
- Die Angabe der Klasse 0 ohne die vereinbarte Spezifikation ist gegenstandslos und entspricht nicht den Forderungen der Norm.
- Verschiedenen Kompressor Hersteller geben an, dass die von ihren ölfreien Kompressoren erzeugte Luft den Anforderungen der Klasse 0 entspricht.
- Bei einem Test des Kompressors unter Reinraumbedingungen werden am Kompressorausgang nur minimale Schmutzstoffmengen festgestellt. Sollte derselbe Kompressor in einer typischen urbanen Umgebung installiert werden, ist der Verunreinigungsgrad hingegen abhängig von der am Kompressoreingang angesaugten Luft. Entsprechend ist die obige Behauptung der Hersteller nicht korrekt.
- Ein Kompressor, der Luft der Klasse 0 erzeugt, muss dennoch mit Filteranlagen sowohl im Kompressorraum als auch am Anwendungspunkt ausgerüstet werden, damit die Reinheit gemäß Klasse 0 in der Anwendung sichergestellt ist.
- Bei Luft für kritische Anwendungen wie beispielsweise Atem-, Medizin-, Lebensmittelanwendungen usw. ist in der Regel lediglich eine Luftqualität entsprechend Klasse 2.2.1 oder 2.1.1 gefordert.
- Die Reinigung der Luft entsprechend einer Spezifikation der Klasse 0 ist nur dann kostengünstig darstellbar, wenn sie am Anwendungspunkt erfolgt.
Kosten senken – Teil 1
Leckagen
Das Leitungsnetz hat die Aufgabe, die Druckluft möglichst verlustarm, d.h. ohne Leckagen und mit möglichst geringem Druckverlust zu den Verbrauchern zu befördern. Druckverluste führen dazu, dass der Verdichter die Luft auf einen höheren Druck verdichten muss als eigentlich erforderlich ist. Ein Druckverlust von 1 bar bei einem Netzdruck von 10 bar verursacht einen Energiemehrbedarf von 7–10%.
Kein Druckluftnetz ist hundertprozentig dicht. Während Leckagen bei Gas- oder Wasserleitungen sofort bemerkt und behoben werden, werden sie bei Druckluft häufig ignoriert.
Die Folge sind erhebliche und vor allem – unnötige – zusätzliche Energiekosten, die zu einer Verschlechterung der Wirtschaftlichkeit führen.
Typische Leckstellen sind:
- Undichte bzw. defekte (Magnet-)Ventile
- Undichte Schraub- und Flanschverbindungen
- Defekte Schläuche und Steckkupplungen
- Fehlerhafte, fehlbediente oder fehleingestellte Kondensatableiter
- Falsch installierte Trockner, Filter und Wartungseinrichtungen
- Korrodierte Leitungen, usw.
Die Reparaturkosten einer defekten Leitung machen dabei gewöhnlich nur einen Teil der Verluste aus. Die Verluste durch Leckagen und eine Möglichkeit, Leckverluste zu bestimmen, sind nachstehend aufgezeigt.
Erfahrungswerte für Leckageverluste:
bei guter Auslegung und Wartung
- Industrienetze: 5–10%
- „raue Betriebe“:15%
- SONST: bis 30% (!)
Druckluftleitungen sind daher sehr sorgfältig zu dimensionieren.
Folgende Kriterien sind zu berücksichtigen:
- Je kürzer die Leitungen, desto geringer der Druckverlust. Die Verdichter sollten also möglichst
- nahe bei den Verbrauchern installiert werden. Nach Möglichkeit sollte die Hauptleitung als
- Ringleitung ausgeführt werden (Druckverluste treten rechnerisch nur auf der halben Rohrleitungslänge auf).
- Der Rohrleitungsquerschnitt muss optimal an den Volumenstrom angepasst werden, da
- Druckverluste quadratisch mit dem Durchsatz wachsen. Große Querschnitte erzeugen geringe
- Druckverluste, sind jedoch teurer und aufwendiger zu installieren.
- Sorgfältige Planung und Ausführung von Leitungsführung, Material und Verarbeitung, da jeder Krümmer, Abzweig oder Schieber - zusätzliche Druckverluste erzeugt.
Wärmerückgewinnung
Kompressoren erzeugen in erster Linie Wärme. Durch diese ungenützte Ressource werden jährlich tausende von Euro sprichwörtlich in die Luft geblasen und unser Klima nachhaltig geschädigt.
Wie auf der Abbildung unten zu sehen, wird die gesamte, zur Erzeugung der Druckluft eingesetzte Antriebsenergie, in Wärme umgesetzt die somit eigentlich bis auf geringe Restanteile zu über 90% für eine Wärmerückgewinnung verfügbar ist. Erste Priorität vor der Wärmerückgewinnung erhält jedoch in jedem Fall die primäre Energiekosteneinsparung durch Verringerung des Verdichtereinsatzes (z.B. Druckluftsubstitution, Lekkagebeseitigung, effizientere Druckluftverbraucher). Diese Aussage wird besonders unter dem Gesichtspunkt anschaulich, dass die Erzeugungskosten für 1 kWh Wärmeenergie lediglich ca. 25% der Kosten für 1 kWh elektrische Energie betragen und die substituierte Wärmeenergie daher deutlich niedriger zu bewerten ist.
Bei der Beurteilung der Realisierbarkeit und der Wirtschaftlichkeit einer Wärmerückgewinnung sind fünf Hauptkriterien zu beachten:
- das Temperaturniveau der Abwärme
- die Gleichzeitigkeit von Wärmeanfall und -verbrauch
- eine möglichst hohe Anzahl von Nutzungsstunden pro Jahr bei gleichfalls hoher
- Verdichterauslastung
- örtliche Nähe von Abwärmeerzeugung und -verbrauch
- Verdichter-Mindestnennleistung: ca. 18,5 kW
Es macht z.B. kaum Sinn, die Abwärme aus einem wassereingespritzten Schraubenverdichter zu nutzen, dessen nahezu isotherme Verdichtung lediglich zu Temperaturerhöhungen von wenigen Graden über Umgebungstemperatur führt.
Die Abbildung unten zeigt die drei am weitesten verbreiteten Möglichkeiten der Wärmerückgewinnung. Auf die Möglichkeit der Abwärmenutzung zur quasi kostenfreien Trocknung der erzeugten Druckluft wird hier nochmals hingewiesen.
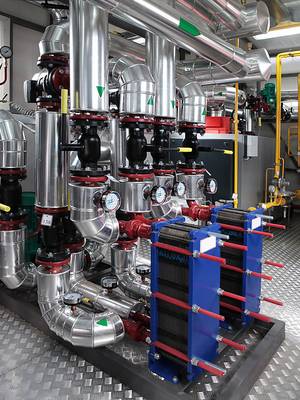
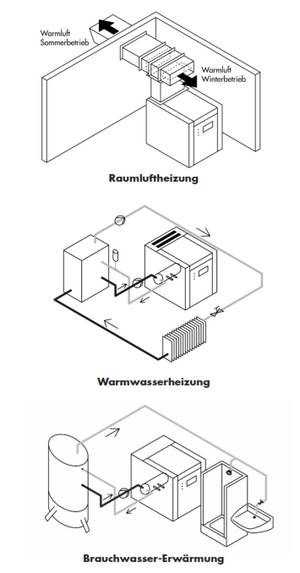
Als einfachste Variante bietet sich die Raumheizung direkt über Zuführung der erwärmten Abluft des Verdichters in die zu beheizenden Räume an. Über eine Klappensteuerung wird diese Heizung bei Bedarf in der kalten Jahreszeit aktiviert, während im Sommer die Abluft ungenutzt ins Freie gelangt. Etwas aufwendiger stellt sich die Raumheizung über ein Warmwassersystem dar.
Hier wird in eine vorhandene Heizwasserleitung ein zusätzlicher Wärmetauscher (Vorwärmer) eingebaut, der den Einsatz fossiler Brennstoffe reduziert.
Mittels einer Fußbodenheizung lässt sich auf diese Weise noch Wärme bei niedrigeren Temperaturen nutzen. Auch in diesen Fällen ist die Nutzungsdauer auf die Heizperiode beschränkt. Fügt man diesem System aber noch eine Brauchwassererwärmung bei, so erhöht sich die Nutzungsdauer und damit die Wirtschaftlichkeit.
In Bsp. oben ist die mögliche Energiekosteneinsparung eines Verdichters mit 37 kW Nennleistung dargestellt. Von der Gesamtleistungsaufnahme (39,8 kW) werden 94% als Heizluft genutzt, was zu einer jährlichen Einsparung von 9.349 Litern Heizöl, entsprechend rund € 1.912, führt. Anhand der Muschelkurven der erforderlichen Jahresbetriebsstunden für eine 2-jährige Amortisationsdauer (Abb. unten) wird deutlich, dass hohe Auslastungsgrade und große Nennleistungen die Zahl der erforderlichen Jahresbetriebsstunden senken. Bei 60% Auslastung reichen beispielsweise 4.000 Jahresbetriebsstunden aus, um mit einer installierten Nennleistung von knapp 75 kW die gewünschte Amortisationszeit zu erreichen.
Betriebskostenaufteilung mit und ohne Wärmerückgewinnung
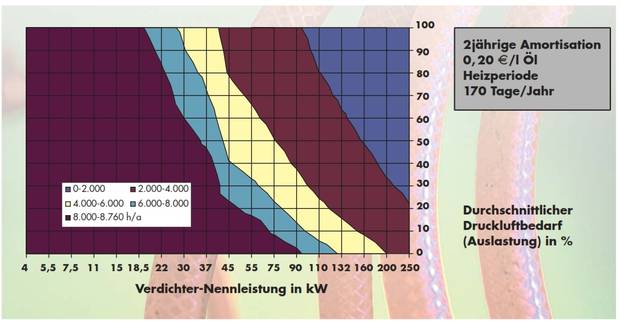
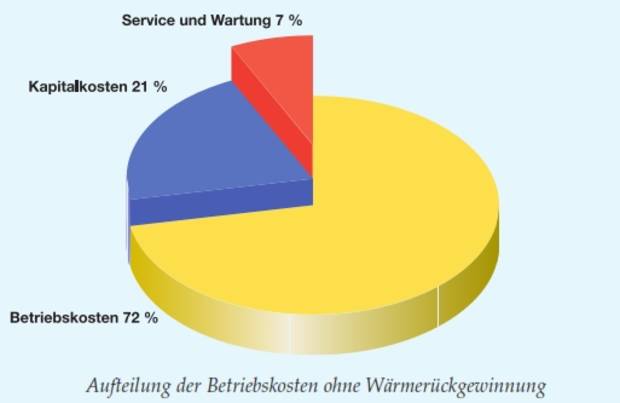
Kosten senken – Teil 2
Druckluft nach Bedarf - Frequenzregelung
Der Druckluftbedarf schwankt in den meisten Betrieben mehr oder weniger stark, je nach Tageszeit, Wochentag oder Zeitraum innerhalb eines Produktionszyklus. Herkömmliche Kompressoren können diesen Bedarfsschwankungen nicht exakt folgen und wechseln deshalb ständig zwischen Last- und Leerlaufbetrieb. Mit der Folge, dass sie in den Leerlaufphasen Energie verbrauchen, ohne Druckluft zu erzeugen. Das aber ist unwirtschaftlich und nicht besonders umweltfreundlich.
Eine optimal konfigurierte Druckluftanlage kann leicht zur Halbierung der Energiekosten beitragen. Effiziente Drucklufterzeugung bedient sich deshalb zunehmend der elektronischen Drehzahlregulierung. Wirtschaftliche Drucklufterzeugung, effiziente Frequenzregelung und effektive Drucklufttrocknung bieten unsere IVR- Kompressoren von 7.5kW bis 160kW Antriebsleistung.
Mit frequenzgeregelten Maschinen sind Druckluftanlagen rund um die Uhr auf wechselnde Anforderungen eingestellt. Ein Kompressor mit Frequenzregelung ist immer dann ideal, wenn der aktuelle Bedarf über die Abdeckung der Grundlast hinausgeht. Leistungsfähige elektronische Steuerungen verbinden geregelte und ungeregelte Kompressoren zu einer bedarfsabhängig arbeitenden Gesamtstation.
Stufenlos einstellbar
Die Frequenzregelung ermöglicht eine sehr breite Liefermengenregelung von 25 bis 100 %. Die Anpassung an den Druckluftbedarf erfolgt durch stufenlose Drehzahländerung des Antriebsmotors, der durch einen Frequenzumrichter angesteuert wird. Gleichzeitig wird dadurch die Drehzahl der Verdichterstufe verändert. Der Frequenzumrichter ermöglicht weiche Starts und Stopps des Antriebmotors. Die Anlaufströme liegen ohne Stromspitzen beim Einschalten im Bereich der Nennströme. Gerade bei größeren Antriebsleistungen ist dies ein Vorteil in der Energiebereitstellung. Sinkt die Liefermenge unter 25 %, arbeitet der Kompressor unwirtschaftlich. Je nach Schaltzyklus schaltet der Kompressor dann aus oder arbeitet im Leerlaufbetrieb weiter. Da ein Schraubenkompressor meist nicht sofort abschaltet, sondern erst für einige Zeit in den Leerlauf geht, wird genau dann unnötig Energie verbraucht. Durch die variable Anpassung der Liefermenge werden Schaltvorgänge und Leerlaufbetrieb aber weitgehend vermieden, so dass der Schraubenkompressor tatsächlich in dem für ihn günstigen Durchlaufbetrieb arbeiten kann.
Idealer Einsatzbereich
Die Leistungsaufnahme eines frequenzgeregelten Kompressors ist – bedingt durch die Verluste des Frequenzumrichters – bei Volllast etwa 3 bis 5 % höher, als die eines ungeregelten Kompressors. Demgegenüber hat die Frequenzregelung jedoch den unbedingten Vorteil, dass bei einer Regelung der Liefermenge durch die Drehzahl des Motors und damit der Drehzahl der Verdichterstufe, die Leistungsaufnahme gleichzeitig nahezu proportional abnimmt. Die Vorteile der Frequenzregelung liegen daher bei der Regelung in kleineren Liefermengenbereichen, wo etwa eine Proportionalregelung (stufenlose Leistungsregelung) über den Ansaugregler unwirtschaftlich arbeitet. Anhand des Vergleichs der beiden Regelkennlinien in der Abbildung erkennt man, dass bei durchschnittlichen
Liefermengen von 100 bis circa 85 % die stufenlose Leistungsregelung über den Ansaugregler Vorteile hat und darunter die Frequenzregelung weit wirtschaftlicher arbeitet. Daraus ergibt sich der ideale Einsatzbereich für die Frequenzregelung bei stark schwankendem Druckluftbedarf bis in kleine Liefermengenbereiche. Durch den sehr breiten Regelbereich bei der Frequenzregelung ist es auch bei kleinem Druckluftbedarf möglich, die Liefermenge diesem Bedarf anzupassen.
Für Spitzenlasten
Durch die Liefermengenanpassung kann der reale Druckluftnetzdruck im Idealfall bis auf 0,1 bar konstant auf dem benötigten Netzdruck gehalten werden. Die bei ungeregelten Kompressoren durch die Differenz zwischen Ein- und Ausschaltdruck vorgegebene Überverdichtung wird so vermieden. Das spart pro bar Höherverdichtung zwischen 6 und 10 % Energie ein. Durch die sehr breite, kontinuierliche Volumenstromregelung ist die Frequenzregelung sehr gut geeignet als Einzelkompressor sowie als Spitzenlastkompressor im Kompressoren Verbund. Bei der Produktion sehr großer Mengen an Druckluft, insbesondere auch ölfreier Druckluft, geht die Rechnung immer dann gut auf, wenn z.B. Turbokompressoren für die Grundlast und regelbare Schraubenkompressoren für die Spitzenlast miteinander in einer Gesamtlösung kombiniert werden.
Einsparungen und Vorteile von Schraubenkompressoren mit Frequenzregelung
- weiche Starts und Stopps in Sekundenschnelle
- kontinuierliche Volumenstromregelung von 25 bis 100 %
- flexible Anpassung der Druckluftliefermenge
- Verschleiß- und Wartungskostenminimierung
- keine Anlaufstromspitzen
- keine unnötige Höherverdichtung
- konstanter Netzdruck +/-0,1 bar
- praktisch fast kein Leerlaufbetrieb
Kompressoren effizient steuern
Trotz der zahlreichen Vorteile ist Druckluft ein äußerst teurer Energieträger und trägt somit deutlich zum Betriebsergebnis bei. Viele Betreiber sind sich nicht bewusst, dass der Löwenanteil der Kosten zum Betrieb einer Druckluftanlage auf die Energiekosten zurück zu führen ist.
Eine Hauptursache dieser Kosten liegt darin, dass die Liefermenge der Kompressoren oft nicht richtig an den schwankenden Druckluftbedarf angepasst wird. So weisen viele Kompressoren nicht selten eine Auslastung von 35- 50 % auf.
In fast allen Kompressoren werden Drehstrom-Asynchronmotoren als Antrieb eingesetzt. Die zulässige Schalthäufigkeit dieser Motoren nimmt mit zunehmender Leistungsgröße ab und entspricht somit nicht der erforderlichen Schalthäufigkeit, die benötigt wird, um Kompressoren mit geringer Schaltdifferenz entsprechend dem tatsächlichen Druckluftverbrauch ein- und auszuschalten. Durch diese Schaltvorgänge werden nur die druckführenden Bereiche des Kompressors entlastet. Der Motor läuft dagegen noch eine gewisse Zeit nach. Die hierfür aufgebrachte Energie ist komplett als Verlust zu betrachten. Der Energiebedarf der Kompressoren liegt während der Leerlaufphase immer noch zwischen 20 -30 % als im Volllastbetrieb.
Darüber hinaus wird von gewissen Kompressoren Herstellern dem Kunden Energie- Einsparpotentiale durch Druckreduzierung (meist bei Anlagen bis 37kW) vorgerechnet, die hernach durch das enge Druckband (Last-/Leerlaufbetrieb) und den festeingestellten Nachlaufzeiten das Abschalten des Kompressors verhindern. Bei sehr vielen dieser Anlagen liegt die Auslastung, trotz integrierten Industrie- PC als Steuerung, lediglich zwischen 30% und 60%. Da diese Anlagen in den allerseltensten Fällen abschalten wird nicht nur der der Geldbeutel des Betreibers übermäßig belastet sondern auch unsere Umwelt nachhaltig geschädigt.
Moderne und effiziente Steuerungs- Managementsysteme schaffen hier Abhilfe und steigern den Wirkungs- und Auslastungsgrad der Anlagen auf 90% und mehr. Die Energieersparnis von mehr als 20% wird sich auf Grund der steigenden Energiekosten immer mehr positiver im Betriebsergebnis auswirken.